Index-velocity and Other Fixed-deployment Instruments
Instruments commonly used for index-velocity and other fixed-deployment current profiling applications are hydroacoustic current meters that use sound transmitted through the water to measure water velocities. For index-velocity applications, the water velocity measured by a hydroacoustic current meter can be used as an estimator or "index" of the mean velocity in a stream or river channel. Other fixed-deployment applications measure a profile of the water-column to determine current patterns in bays, harbors, estuaries, lakes and rivers.
Hydroacoustic current meters used by the USGS for index-velocity and fixed-deployment current profiling applications include:
Acoustic Doppler Velocity Meters
Description
Acoustic Doppler Velocity Meters (ADVMs) are acoustic current meters that use the Doppler principle to measure water velocities in a two-dimensional plane. These instruments are currently (2012) the most commonly used velocity meter for index velocity stations. Each ADVM transducer transmits sound pulses of a known frequency along a narrow acoustic beam (fig 1). As the pulses travel along the acoustic beam, they strike particulate matter (scatterers) suspended in the water. When the pulses strike scatterers some of the sound is reflected along the acoustic beam to the transducer. The reflected pulses have a frequency (Doppler) shift proportional to the velocities of the scatterers they are traveling in along the acoustic beam:
V = (Fd/2Fs)*C
where,
Fd is the Doppler shifted frequency received at the
transducer,
Fs is the transducer transmit frequency,
C is the sound speed, and
V is the scatterer (water) velocity.
ADVMs have two acoustic beams set at a known angle (beam angle) in a
two-dimensional plane that is parallel to the water surface so if seen
from
above they would be in a "V" configuration (fig 1). From the beam
radial velocities (velocities measured along the acoustic beams) the
ADVM uses
trigonometry to compute velocities in a user-set sample volume (fig
1).
Velocities are output in cartesian coordinatates; in a typical
installation
where the ADVM is mounted on the side of the river, the x-component is
the
component of velocity parallel to the main flow direction of the river
("along flow") and the y-component of velocity is perpendicular to
the main flow direction ("across flow") (fig 1).
Figure 1. ADVM Schematic
The ADVM-measured velocity used to index
mean velocity is usually the sample volume x-component of velocity. If
an ADVM
is equipped with multiple sample volumes, the average x-component of
velocity
from more than one sample volumes can be used as the index mean
velocity.
ADVM transducer frequency, maximum and minimum sample volume sizes,
and
features vary by manufacturer and model. AVM features can include:
- multiple sample volumes
- "upward-looking" transducers to measure water stage
- internal data storage capability
- SDI-12 data communications specification
- internal tilt and roll sensors
Instruments
The following is a brief description of some common ADVM models along with links to manufacturer specifications:
Sontek Argonaut SL – A 2D side-looking velocity meter intended for side-looking current or flow measurement operations from bridge piers or pilings;
Sontek Argonaut SW - Typically mounted on the bottom of a channel, stream, or pipe, and measures water level and vertically integrated velocity in small channels from 0.5 to 16ft (0.3-5m) deep; Link: http://www.sontek.com/iq Various models of the IQ exist, the IQ Standard, the IQ Plus, and the IQ Pipe.
RD Instruments Channel Master - A 2D side-looking velocity meter intended for side-looking current or flow measurement operations from bridge piers or pilings;
Ott SLD - The OTT SLD is an acoustic Doppler sensor system for continuous measurement of flow velocity and optional water level in rivers and channels.
Acoustic Doppler Profilers
Description
Acoustic profilers use the Doppler frequency shift of acoustic pulses reflected from particles in the water to measure water velocities in multiple sample cells. Profilers can be mounted in a horizontal orientation (fig. 1a) to measure velocity profiles across a channel or mounted in a vertical orientation (fig. 1b) to measure vertical velocity profiles. A profiler uses two to four transducers set at a known orientation to measure water velocities. Each transducer transmits sound pulses of a known frequency along a narrow acoustic beam (fig 1). As the pulses travel along the acoustic beam, they strike particulate matter (scatterers) suspended in the water. When the pulses strike scatterers some of the sound is reflected along the acoustic beam to the transducer. The reflected pulses have a frequency (Doppler) shift proportional to the velocities of the scatterers they are traveling in along the acoustic beam:
V = (Fd/2F0)*C
where,
Fd is the Doppler shifted frequency received at the transducer,
F0 is the transducer transmit frequency,
C is the sound speed, and
V is the scatterer (water) velocity.
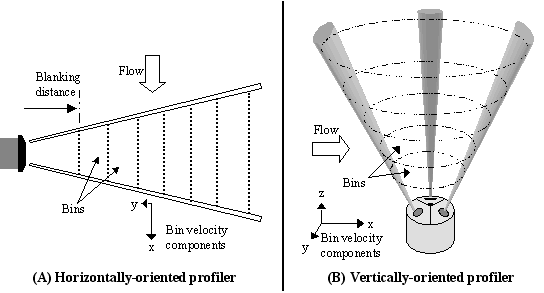
Figure 1. Examples of acoustic profiler orientations
Profilers measure velocities in
uniformly-sized cells or bins along the acoustic beams (fig 1). By
measuring
velocities in a number of bins across a channel or vertically through
the water
column, these instruments produce horizontal or vertical water velocity
profiles, hence the designation "profiler."
Profilers have varying acoustic beam geometries and can be installed in
several
different orientations. Profilers with two acoustic beams are usually
used for
horizontal orientations; the beams are set in a two-dimensional plane
that is
parallel to the water surface so if seen from above they would be in a
"V" configuration. In the example orientation shown in figure 1a, the
profiler is mounted on the side of the river and velocities are output
in
cartesion coordiates; the x-component is the component of velocity
parallel to
the main flow direction of the river ("along flow") and the
y-component of velocity is perpendicular to the main flow direction
("across
flow"). The profiler outputs an x-component and y-component of velocity
for each bin (the number and size of the bins is programmable). An
x-component
and y-component velocity can be output for each bin.
Profilers with three acoustic beams are usually used for vertical
orientations
with the the three beams traversing the water column from the bottom up
for a
profiler mounted on the channel bottom (fig 1b), or from the top down if
the
profiler mounted on a floating buoy. Profilers with three beams can
output
velocities in three dimensions. In the example shown in fig. 1b, the
profiler
outputs velocities in cartesian coordinates; with the x-component is
along
flow, the y-component is cross flow, and the z-component is the
vertical-velocity component (up or down). All three components can be
output
for each bin.
The profiler-measured velocity used to index mean velocity can be the
velocity
measured in one or multiple bins.
Profiler transducer frequency, maximum and minimum range, maximum and
minimum
bin size, and features vary by manufacturer and model. Profiler features
can
include:
- internal tilt and roll sensor
- internal compass
- dynamic ranging, a feature that adjusts the range to uppermost bin based on the distance to the water surface
- internal data storage capability
- a fourth beam that produces a redundant vertical velocity to test the assumption of homogenous flow in all beams
- a pressure transducer for estimating water stage
Instruments
The following is a brief description of some common models of acoustic Doppler profilers along with links to manufacturer specifications:
Sontek Argonaut XR - A 3D low-profile velocity profiler with adjustable sampling volume size and location
Sontek ADP - A 3-beam current profiler available in various frequencies
Teledyne RD Instruments Monitor – A 4-beam direct-reading ADCP that is typically bottom frame-mounted and hard-wired to shore to provide real-time monitoring of coastal currents.
Teledyne RD Instruments Rio Grande – A 4-beam ADCP primarily used as a rapid-sampling current profiler designed to operate from a moving boat but have also been used in upward and downward-looking fixed applications.
Acoustic Velocity Meters
Description
Acoustic Velocity Meters (AVMs) are time-of-travel devices that measure water velocities along an acoustic path between pairs of transducers located on a diagonal line across a channel. The transducers are connected to a central processors by cables (figure 1). Acoustic pulses are transmitted along the acoustic path; the upstream-moving (against current) pulses travel slower than the downstream-moving (with current) pulses. The difference in travel times between the upstream and downstream moving pulses is proportional to the water velocity.
Figure 1. AVM Schematic
The AVM measures the average water velocity along the acoustic path (VP, figure 1); then computes the "line velocity," the velocity component parallel with the average downstream flow line (VL):
VL = (B/2cosA)(1/TDC-1TCD)
Where,
VL is the AVM line velocity,
B is the length of the acoustic path (figure 1),
A is the angle between acoustic path and VL (figure 1),
TDC is the travel time from transducer D to transducer C (figure
1), and
TCD is the travel time from transducer C to transducer D (figure
1).
AVMs can have multiple configurations, including:
- Multiple paths in the horizontal; the "cross-path" configuration (figure 2a) is commonly used. Multiple paths in the horizontal; the "cross-path" configuration (figure 2a) is commonly used.
- Multiple paths in the vertical (figure 2b). Multiple paths in the vertical can define vertical velocity profiles and can identify flow stratification.
- Reflector configuration (figure 2c). For sites where running cables to the far-bank transducers is impractical, it is possible to have both acoustic path transducers on one side of the channel. The acoustic pulses are bounce off of a reflector mounted on the opposite side. Reflectors are typically constructed of metal plates welded together so that the angle between plates is 90 degrees.
- Responder configuration (figure 2d). Another alternative for sites where running cables to the far-bank transducers is impractical is to have a responder mounted on the side of the channel opposite to the transducers. A responder is connected to two transducers; signals transmitted from transducer A are received at transducer B and immediately replicated and transmitted by the responder from transducer C to transducer D figure 2d). The total upstream travel time is computed for signals traveling along path ABCD and the downstream travel time is computed for signals traveling along path DCBA.
Figure 2. AVM configurations
The AVM-measured velocity used to index
mean velocity can be the line velocity from one acoustic path or from
multiple
acoustic paths. For example, if the horizontal angle of flow in the
channel is
constant, the AVM line velocity from one acoustic path may be sufficient
to
accurately index mean velocity. If the horizontal angle of flow in the
channel
changes over time, using the average of AVM line velocities from both
acoustic
paths of a cross-path configuration (fig 1a) may be a more accurate
index of
mean velocity than the velocity from a single path.
AVM transducer frequency, maximum number of acoustic paths, maximum and
minimum
acoustic path lengths, and features vary by manufacturer and model. AVM
features can include:
- "upward-looking" transducers to measure water stage
- internal data storage capability
- SDI-12 (serial digital interface) data communications specification (allows interface with many types of electronic data loggers)
Instruments
Kern Elektronik AG- maker of AFFRA and Deltaflex AVMs (formerly made by Stedtnitz Maritime Technology).
Sonicflow - AVM manufactured by Ott
ADS Environmental Services- products include several lines of AVMs